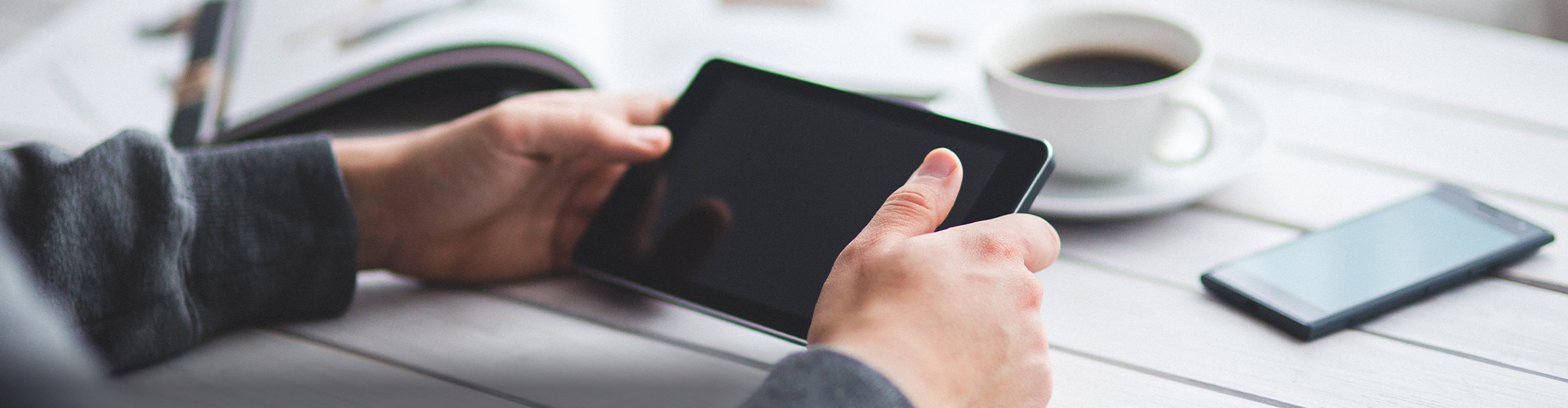
More Option
Structure and Working Principle of Hydraulic Rock Drill
BY: react360
3 months ago
The hydraulic rock drill is an efficient rock-breaking tool widely used in mining, tunnel excavation, and construction engineering. Powered by a hydraulic system, it achieves rock fragmentation through high-frequency impact and rotary motion. This article will provide a detailed introduction to the structure and working principle of the hydraulic rock drill.
1. Structure of the Hydraulic Rock Drill
The hydraulic rock drill typically consists of the following main components:
- Hydraulic System
The hydraulic system is the core power source of the rock drill, including a hydraulic pump, oil tank, control valves, hydraulic motor, and hydraulic cylinder. The hydraulic pump converts mechanical energy into hydraulic energy, and control valves regulate the flow and pressure of hydraulic oil to drive the impact and rotation mechanisms. - Impact Mechanism
The impact mechanism generates high-frequency impact forces and usually comprises a piston, impact cylinder, and distribution valve. Hydraulic oil drives the piston to reciprocate within the impact cylinder, producing powerful impact energy that is transferred to the drill rod and bit to break the rock. - Rotation Mechanism
The rotation mechanism, driven by a hydraulic motor, rotates the drill rod and bit to improve drilling efficiency and prevent sticking. It typically includes a gear transmission system and a hydraulic motor. - Drill Rod and Bit
The drill rod connects the impact mechanism to the bit, transmitting force. The bit directly contacts the rock,承受冲击和旋转力。根据岩石硬度,可选用不同类型的钻头,如十字型或球齿型。承受冲击和旋转力。根据岩石硬度,可选用不同类型的钻头,如十字型或球齿型。withstands impact and rotational forces. Different bit types, such as cross or button bits, are selected based on rock hardness. - Frame and Propulsion Mechanism
The frame provides structural support for the rock drill, while the propulsion mechanism (typically a hydraulic cylinder or chain system) advances the drill forward, maintaining contact pressure between the bit and the rock. - Cooling and Lubrication System
To prevent overheating and component wear, the rock drill is equipped with a cooling system (usually oil- or water-based) and a lubrication system, ensuring long-term stable operation. - Control System
Modern hydraulic rock drills often feature electro-hydraulic control systems, utilizing sensors and controllers to enable automated operation, improving precision and safety.
2. Working Principle of the Hydraulic Rock Drill
The working principle of the hydraulic rock drill is based on the conversion of hydraulic energy and the transmission of mechanical energy. The main workflow is as follows:
- Generation and Distribution of Hydraulic Energy
The hydraulic pump draws hydraulic oil from the tank and pressurizes it. The oil is then distributed to the impact and rotation mechanisms via control valves. The valves adjust oil pressure and flow based on operational needs, ensuring coordinated impact and rotation actions. - Impact Action
In the impact mechanism, high-pressure hydraulic oil drives the piston to reciprocate rapidly within the impact cylinder. The piston’s motion is controlled by the distribution valve, causing it to periodically strike the drill rod’s tail. The impact energy is transmitted through the drill rod to the bit, which strikes the rock surface, creating localized stress concentration and fracturing the rock. - Rotation Action
Simultaneously, the hydraulic motor drives the rotation mechanism, causing the drill rod and bit to rotate at a specific speed. This rotation changes the impact point of the bit, expanding the breaking area and preventing the bit from getting stuck in rock crevices. - Propulsion and Drilling
The propulsion mechanism applies constant pressure via a hydraulic cylinder or chain system, pushing the rock drill forward to maintain close contact between the bit and the rock. As the rock breaks, the bit gradually penetrates, forming a borehole. - Debris Removal and Cooling
During drilling, rock debris is expelled from the borehole using high-pressure water or compressed air to prevent clogging. The cooling system dissipates heat from the hydraulic oil and key components, while the lubrication system reduces frictional wear.
3. Advantages of Hydraulic Rock Drills
Compared to traditional pneumatic rock drills, hydraulic rock drills offer the following advantages:
- High Efficiency and Energy Saving: The hydraulic system has a high energy utilization rate, delivering superior impact force and drilling speed.
- Precise Control: Electro-hydraulic control systems enable automation and remote operation, reducing manual labor intensity.
- Strong Adaptability: Impact frequency and rotation speed can be adjusted based on rock type and project requirements.
- Low Noise and Vibration: The hydraulic system operates smoothly, minimizing disturbance to operators and the surrounding environment.
4. Application Scenarios
Hydraulic rock drills are widely used in the following fields:
- Mining: For drilling blast holes and anchor holes.
- Tunnel Engineering: Critical for metro, railway, and highway tunnel excavation.
- Construction Engineering: Used in foundation pile holes and ground treatment.
- Geological Exploration: For core sampling and geological analysis.
5. Conclusion
The hydraulic rock drill, with its efficiency, precision, and reliability, is an essential tool in modern rock excavation. Its complex yet sophisticated design integrates impact and rotation actions through precise hydraulic control, achieving efficient drilling. In the future, with advancements in automation and intelligent technologies, the performance and application scope of hydraulic rock drills will continue to expand.
Share On
Search
Browse By Categories
Recent Posts
Contact You
To ensure we can follow up on your inquiry effectively, could you please provide your email address?